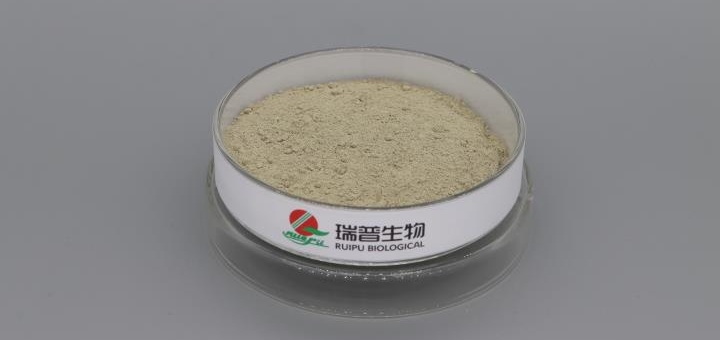
Ferrous gluconate, as an iron supplement with good water solubility and high bioavailability, its preparation process needs to balance reaction efficiency, product purity, and production costs. The core is to generate the target product through chemical reactions between gluconic acid and ferrous salts, and to reduce impurities and improve yield through process optimization. The following analysis focuses on preparation processes and optimization strategies:
I. Main Preparation Processes of Ferrous Gluconate
Ferrous gluconate is synthesized through neutralization or displacement reactions using gluconic acid (or its derivatives) and ferrous salts as raw materials. Common process routes include:
Direct neutralization of gluconic acid with ferrous salts
Using gluconic acid and iron powder (or ferrous sulfate, ferrous chloride) as raw materials, displacement or neutralization reactions occur in aqueous solutions. For example, when gluconic acid reacts with iron powder, the iron powder acts as a reducing agent to maintain Fe²⁺ in its reduced state. The reaction formula can be expressed as:
2C₆H₁₂O₇ (gluconic acid) + Fe → Fe(C₆H₁₁O₇)₂ (ferrous gluconate) + H₂↑.
The reaction must be carried out under the protection of inert gas (such as nitrogen) to prevent Fe²⁺ from being oxidized. Meanwhile, temperature (60–80°C) and pH (3.0–4.0) are controlled to promote complete reaction and reduce Fe²⁺ hydrolysis. After the reaction, excess iron powder is removed by filtration, and the filtrate is concentrated and cooled to crystallize the product.
Gluconolactone hydrolysis-ferrous salt reaction method
Gluconolactone (GDL) slowly hydrolyzes in water to form gluconic acid (C₆H₁₀O₆ + H₂O → C₆H₁₂O₇). Taking advantage of this property, GDL can be first dissolved and hydrolyzed, then ferrous salts (such as ferrous sulfate) are added, and pH is adjusted (usually with sodium hydroxide) to allow gluconate ions to combine with Fe²⁺. The advantage of this method is that the hydrolysis rate of GDL is controllable, reducing Fe²⁺ oxidation caused by intense local reactions, making it suitable for large-scale production.
Electrosynthesis method
Using glucose and ferrous salts (such as ferrous sulfate) as raw materials, under the action of direct current in an electrolytic cell, glucose is oxidized to gluconic acid at the anode, while Fe²⁺ combines with gluconate ions at the cathode to form ferrous gluconate. This process does not require additional oxidants or reducing agents, resulting in high product purity. However, it is necessary to precisely control the electrolysis voltage (2–3V), current density, and reaction time to avoid excessive oxidation of glucose or oxidation of Fe²⁺ to Fe³⁺ at the anode.
II. Optimization Strategies for Preparation Processes
The core challenges in preparing ferrous gluconate are inhibiting Fe²⁺ oxidation, improving product purity and yield. Specific optimization directions are as follows:
Oxidation protection of the reaction system
Inert gas protection: Nitrogen or carbon dioxide is introduced throughout the reaction to exclude oxygen from the system. Especially in high-temperature reaction stages (above 60°C), although oxygen solubility decreases, Fe²⁺ oxidation activity increases, so gas protection must be strengthened (such as using a sealed reactor with continuous exhaust).
Adding reducing agents: A small amount of ascorbic acid (vitamin C) or sodium sulfite is added to the reaction system. Their reducibility reacts with oxygen preferentially, indirectly protecting Fe²⁺. For example, when the addition amount of ascorbic acid is controlled at 0.5%–1% of the raw material mass, the Fe²⁺ retention rate can be increased by 15%–20% without introducing harmful impurities.
Precise control of reaction conditions
Balance between temperature and time: Increasing temperature can accelerate the reaction rate (e.g., increasing from 40°C to 60°C can shorten the reaction time by 30%), but it also accelerates Fe²⁺ oxidation. Therefore, the appropriate temperature should be selected according to the type of raw materials (e.g., 50–55°C is suitable for the reaction between gluconic acid and iron powder, while 60–65°C can be used for the GDL hydrolysis method). The reaction endpoint is determined by monitoring the system potential (Fe²⁺/Fe³⁺ electrode potential) to avoid over-reaction.
pH control: Fe²⁺ is most stable under weakly acidic conditions (pH 4.0–5.0). If pH is too low (<3.0), it will inhibit the combination of gluconate ions and Fe²⁺; if too high (>6.0), it will easily cause Fe²⁺ hydrolysis to form ferrous hydroxide precipitation. Dilute sulfuric acid or sodium hydroxide solution can be added dropwise to dynamically adjust pH. For example, in the GDL hydrolysis-ferrous salt reaction, gradient pH adjustment (maintaining pH 3.5–4.0 to promote GDL hydrolysis first, then increasing to 4.5–5.0 to promote product formation) can increase the yield by more than 10%.
Optimization of product separation and purification
Improvement of crystallization conditions: After the reaction, the solution concentration is increased by evaporation and concentration (vacuum reduced-pressure concentration, temperature ≤60°C to avoid Fe²⁺ oxidation), then gradient cooling crystallization is adopted (e.g., slowly cooling from 50°C to 5°C at a rate of 2–3°C/h) to promote the formation of larger ferrous gluconate crystals and reduce impurity inclusion.
Washing and drying processes: The crystallized product is washed with an ethanol-water mixture (volume ratio 1:1), which can not only remove residual soluble impurities such as glucose and ferrous salts but also reduce Fe²⁺ oxidation during washing (ethanol can reduce dissolved oxygen in water). For drying, vacuum freeze-drying or low-temperature blast drying (40–45°C) is used to avoid Fe²⁺ oxidation and crystal structure damage caused by high temperatures.
Improving adaptability of raw materials and equipment
Raw material purity control: High-purity gluconic acid (content ≥98%) or GDL (purity ≥99%) is selected to avoid heavy metal ions (such as Cu²⁺, Mn²⁺) in raw materials, which act as catalysts to accelerate Fe²⁺ oxidation. For ferrous salts, food-grade ferrous sulfate is preferred due to its high solubility and easy separation of sulfate ions through crystallization.
Equipment material optimization: Reactors, pipelines, and other equipment are made of stainless steel (type 316L) or glass-lined materials to avoid impurity dissolution from iron equipment and reduce the catalytic effect of metal surfaces on Fe²⁺ oxidation (e.g., copper and zinc ions significantly accelerate Fe²⁺ oxidation).
Through the above strategies, the yield of ferrous gluconate can be increased from 70%–80% in traditional processes to over 90%, with Fe²⁺ content stably above 98%, meeting food-grade or pharmaceutical-grade standards. In addition, combined with green chemical concepts, unreacted raw materials (such as gluconic acid) in mother liquor can be recycled to further reduce production costs and improve process economy and sustainability.